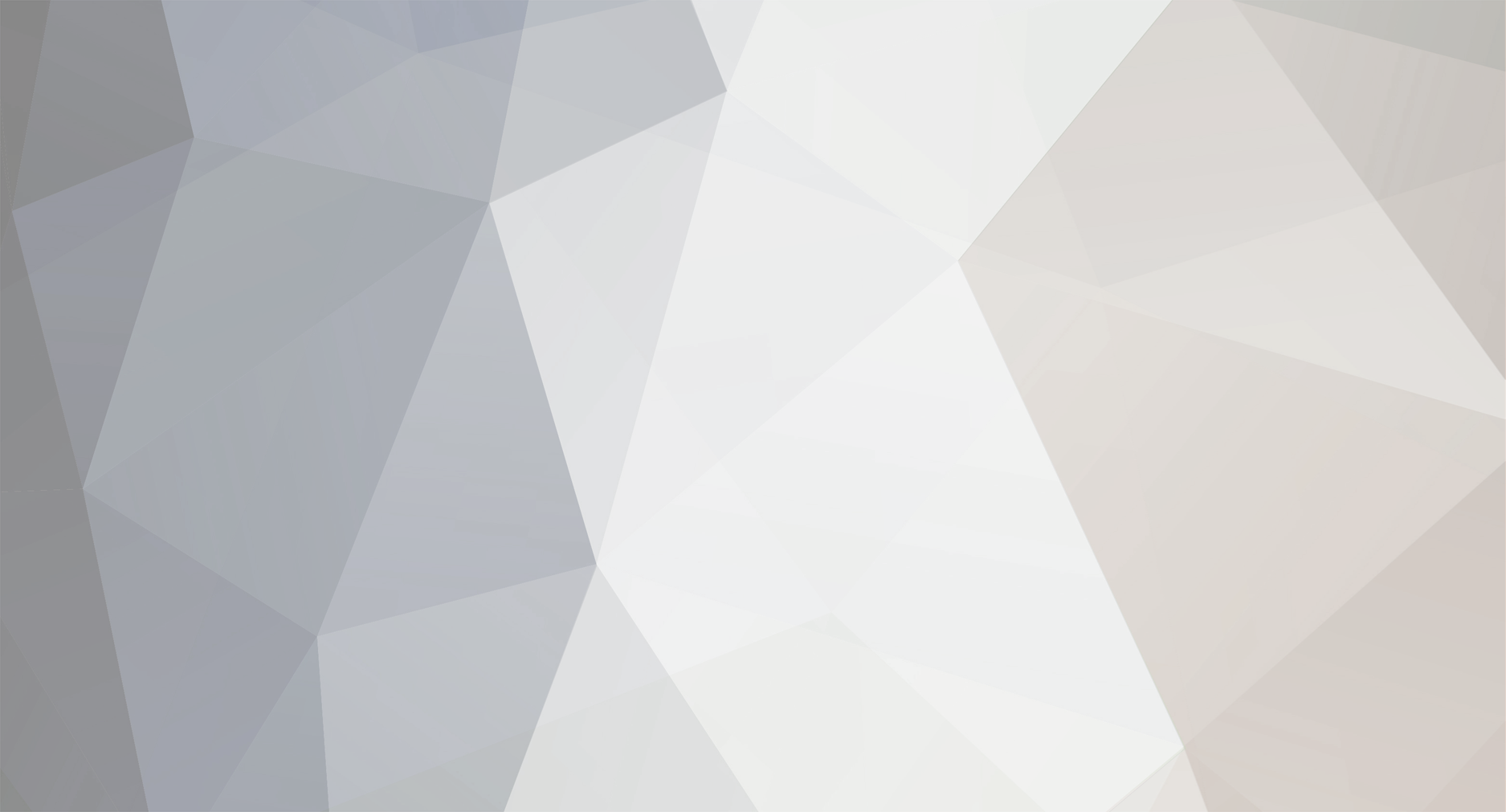
schizek
Members-
Posts
49 -
Joined
-
Last visited
Content Type
Profiles
Forums
Blogs
Downloads
Articles
Gallery
Everything posted by schizek
-
Is it possible to create custom embosses for sheet metal use. Preferably to edit the cross section of a standard emboss into the desired shape. What is the easiest way to achieve this. Example: stamping of the chevrolet bow tie symbol into a peice of sheet metal.
-
Thanks Shaun Two more quick questions: What do you consider "large seat" IronCAD installations? Is there a date that ASTI has tageted for release of their version?
-
I would also like to know more about this. The piece I am most interested in is the check in/check out function. For one reason, when you have multiple people working on files that have the same parts linked into them, the "open as a copy" to parts that are already being used gets very confusing. Also, just the ability to know in an assemble that you are only modifying that assembly and NOT any other individual parts accidentally would be a huge help.
-
So, NOBODY uses TeamVault? Nobody from IronCAD with ANY feedback? Interesting.
-
What is the status of TeamVault. Is anybody using it? Is the check in/out feature going to be incorporated into a new IronCAD version? I would love to know what the scoop is.
-
Just upgraded to PU2. It looks like the save command also compresses the file. That's what I needed. Good Fix
-
Although I am sure this happens with linked assemblies too, I am only talking about individual parts. I think it is the same concept though. We are running 6.0 but are not at PU2. Will this fix the problem? I would want to compress the file right along with just saving the file, is this the case?
-
Question about file sizes. IronCAD scene files do not seem to compress when saving. If you do a "save as" to a different file name, delete the old file, and rename the new file to the original name it will compress. Is there a better, more user friendly way to reduce file sizes?
-
If you use cut sheet metal in certain bend areas, the unfolded sheet metal thickness is cut at an angle, which is not correct. The idea of getting it to fold properly is important, but just as important, if not more important, is being able to create the proper unfolded sheetmetal.
-
The cut sheet metal tool doesnt always work to give you the correct information. It is basically cutting the sheet metal AFTER form, when in reality the sheet metal is cut BEFORE form. I know it doesn't sound like much, but it is a big deal when you are trying to get correct blanks.
-
Here you go,......hopefully modifyaffected.ics modifyaffected.ics modifyaffected.ics modifyaffected.ics modifyaffected.ics modifyaffected.ics
-
Attached is a file of what I am talking about. One custom profile that includes 3 notches does not work if you try to modify affected bends, but if you do all 3 separately, they do work. It is a lot cleaner if you were able to do this, not only for accuracy but also for tree size. modifyaffected.ics
-
Can anybody tell me the use of postioning a cutout and NOT have that punch positioned with respect to the flat. I see that it is the default, but I don't see a need or benefit to not have it this way all the time. That being said, just because it is positioned with respect to the flat does not give it the ability to MODIFY that cutout in the unfolded sheet. In reference back to my original V-Notch, there are no cutouts creating that, there are some modified cross sections, after unfolding I would like to take this notch that is created and form it to be consistant with our tooling. If I tried to create that as a custom shape......yeah right, like I could get the modify affect bends to work across all of those bends. This is just one prominent example of the need to modify the unfolded sheetmetal. I know I harp on this issue over and over, but it was promised long ago when we first bought into IronCAD, and it still is not where we need it. As a predominantly sheetmetal company, this issue is far and away the most important issue we face. Although I feel IronCad is one of the best CAD systems out there for mid range modelers, this issue is important enough to force us to go away from IronCAD if it is not addressed.
-
So.......Is this something that is not possible? Is it a memory problem? Graphic problem? Other?
-
I guess I am confused about the possibility of positioning cutouts in the flat. If you position a cutout in the flat, it doesn't stay that way in the form, correct? Am I missing something that I could be doing here to accomplish this?
-
Attached is a sample of a notch we are trying to create. The notch needs to be a standard V notch (not what I have modeled here) at a certain depth. What I would like to do is create it as I have in the folded state, unfold it, and modify that notch to be what the actual cutout should be like, and refold the part KEEPING that information. Wim, you stated that "There are situations that I would like to position a cutout in the flat, and that is possible right now" I do not beleive this is true, what I see is any changes done to the flat are lost after refolding. I understand that modifying the folded is needed when trying to locate certain features on a part. but there are just as many times that it is the opposite and the folded result does not matter (i.e. the file i have attached, it doesnt really matter what the folded corner looks like, but it absolutely HAS to be a V notch at a given depth. vnotch.ics vnotch.ics
-
I am trying to create a custom profile that wraps around a sheet metal bend. My problem is, the custom profile is more of a pattern, and has several separate notches that consist of one custom profile. When I try to modify the affected bend for it to wrap, it disappears. Is this the intended functionality?
-
This process should be able to be done in the flat and then refold the sheet, not modifying the folded part in order to create the flat. I think the thinking is backwards here, or at LEAST we should have both options available.
-
Thanks, that is the info that I wanted, just couldn't find it. FYI it is on page 603 of "Technical Drawing" 9th edition by Giesecke
-
What I am curious to know is.....what is the "standard" for an isometric view. I am assuming you take a front view and rotate that part in 2 axis. I want to know what that rotation is. Basically, if I want to create an Isometric view in another software package to match IronCAD, how would I do that.
-
Can anybody tell me what the rotation in the X,Y, and Z axis' are to generate the Isometric(TFL, TFR, BFL, BFR) views. Is this something that can be modified if desired?
-
The cut sheet metal tool is OK for some options, but it is not accurate. It cuts the sheet metal AFTER it is formed instead of before it is formed. If you cut sheet metal on a bend, it will cut into that metal at an angle and be incorrect. I really hope developers are working on providing the ability to modify a sheet metal part in either the flat or the folded state for the next release.
-
That would work, but would be very time consuming. I am showing the assembly of units that use up to 75 bolt or screws. That is a lot of view editing.
-
A screw does NOT have to have a cross recess to put it in, the hex head gives it that capability. I understand that I can put a slot in the screw and then delete that recess (as well as create my own fastener catalog when complete), so I do have a work around. This should probably go to an enhancement request now. There are Hex head screws WITHOUT a cross recess, a simple box for NONE in the cross recess type could accommodate this, without having to modify existing screws or create a separate catalog.
-
That works, but it should be an option in the properties.