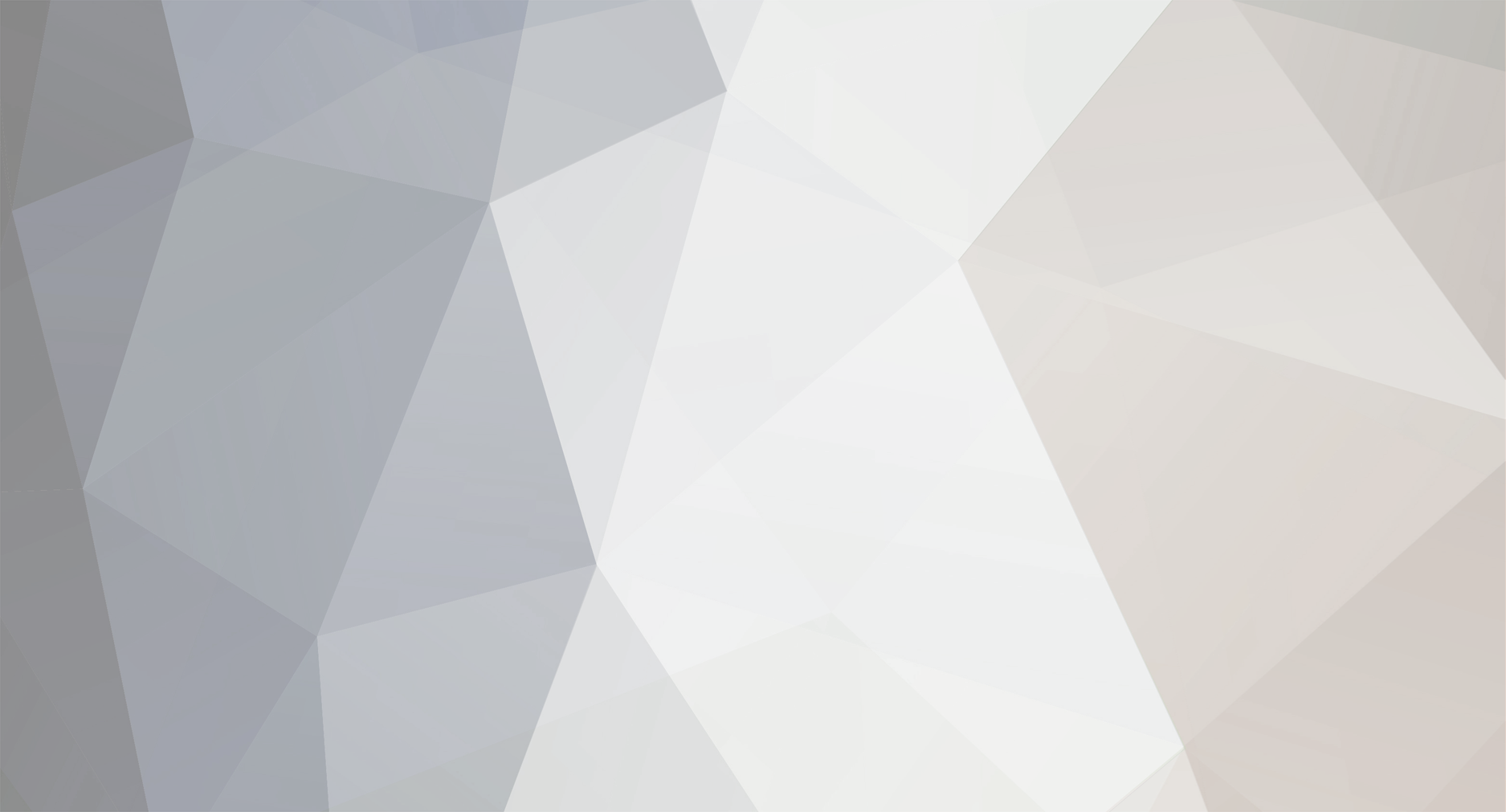
MRAHM
Members-
Posts
310 -
Joined
-
Last visited
Content Type
Profiles
Forums
Blogs
Downloads
Articles
Gallery
Everything posted by MRAHM
-
If it was possible to choose within IronCAD it would be faster and in my opinion simplier. I´m happy everytime I don´t need to use catalogs. They are slow to work with. IC2020 is better with the possibility to have multiple catalogs active. Thanks for your tip!
-
Thanks Cary for a solution!
-
Hello In order to get correct BOM list I need to use the "Treat as part" function. This works great but when there is multiple instances of an assembly we need to repeat the procedure many times. Check movie about the issue. Select many assemblies and apply this configuration one time would be helpfull. /mikael 200317_10-27_298.mp4
-
Thanks for the info. Can you build an update to next version function? I think that would save users from much frustration. /Mikael
-
I used to be in manufactoring. Sometimes there was a geomtrical error in the part that made the CAM software go crazy. One easy fix was to export the modell (to step, acis, _xt) and then import it in IronCAD and then export it again. This helped me many times. My guess is that an export/import would help in our case as well. /micke
-
I found this function when messing around with positioning intellishapes. Maybee it is just me that it took looooong time to find it but I think it is powerfull and smart. It works so good that I haven´t noticed it! When dropping Intellshapes onto other intellishapes the position is relative to the anchor point of each shape. Look in the video how it is possible to move several shapes but only selected the "base". When the dropped feature no longer is in contact with the "base" shape it also looses it relative relationship. I found that it is that the Anchor point is set to "Attach to Surface" that make this happens. One strange thing is that if I make the hole pattern with pattern instead of links it does´t work. I like this! Good function that works without any extra fiddeling around or thinking! Position_Intellishapes.zip
-
Thanks for your help! I was shure that I did like you sad but I must have made something wrong.
-
Hi When using Smart Dimension to position intellishapes I often get the intellishapes twisted in any way. What am I doing wrong? I have tried to put the dimension on edges and faces but still the model is´t looked in the way I wan´t to. /micke
-
GREAT with the new online manual and Youtube channel for IronPRO! You find it in the toolbar for each IronPRO catalog in the latest release.
-
I think that the trouble is the geometric kernel. From what I know Parasolid and Acis only works on Windows. IF I remember both Parasolid and Acis is single threaded due to the complexety to rewrite them. I gues it can be a lot of work to port them to another system that have smaller marketshare. OpenCascade and Ascon has both geometric kernels that runs on Windows, Linux and OsX. Opencascade is multithreaded with helps you get the most out of your new multi Core computer. The kernel is limiting because it is the brain. The hole CAD application is developed around the kernel. But beside the kernel there is nothing that could´t been written in such a way that a CAD system is platform independent. From my point of view it is bad habbit to write for one OS. And when we today see that Andoid has 80% marketshare in phones and is released 2007 we just can guess what happens in 5-10 years for desktop computers. Microsoft is still biggest on desktop computers but I would focus on web and platform independency for the future. But the market rules. My CAM software is written in Delphi which is platform independent but it is only released for Windows. The hole CAD/CAM industri thinks Windows. And even if I prefer Linux and osx Windows is a great OS that has become better over the years. /micke
-
Thanks! Then it is Windows related and not IC.
-
Hi Is there anyone else who have updated windows to W10? My experience is that IronCAD has become slow after update from W7 to W10. Unfortunatly IC was updated in the same time frame so I can´t realy tell if it is IC or Windows that is slow. Has anyone else updated to W10? Is latest version of IC working for you? /micke
-
Working with Sheetmetal Fabricators WorkFlow?
MRAHM replied to tlehnhaeuser's topic in General Discussion
About the K-factor. I know that some set up different k-factors for different vendors. But this is all based on their experience and how critical the result is. -
-
Connect Keyboard to a command in IRONCAD
MRAHM replied to Robert Andersson's topic in Tips and Tricks
Is there a export/import function for your settings between IC versions? -
Working with Sheetmetal Fabricators WorkFlow?
MRAHM replied to tlehnhaeuser's topic in General Discussion
Hi Check with your vendor what they prefer. The vendor I normally use uses Bycut by Bystronic in their cutting machine. So I can send and unfolded parasolid and their program do the rest. It is easiest for all of us. Bycut is a SolidWorks extension so if they get a parasolid file they can do all measurements they need and even make adjustments if needed. In this case I only supply a course drawing just to make shure no scaling problems occour. If you find a good vendor use them! When you have learned how they want the files/drawings etc then it all becomes easier. -
Hello I´ve been using IronCAD for a while and everytime I try another CAD software I realize why I choosed IronCAD. There are some bugs and errors but the way of designing is powerfull! Anyway...there are some issues. I scrolled throught the enhancement request and bug fix topics and many things seems to be related to to little testing. It always is some may say.... Most bugs are not huge and affect stability, most of them are small and irritating. Now to the point. I would like an option to be a beta tester. Some people realy like to test features and functions. Can´t you enable that option in the update feature that IC has. Then they can download updates and bugfixes much more often and help you test it before the release of the next SP. /micke
-
Hi Do anyone of you know how to get UserName to inherit value from PartNumber and/or Description? By using PartNumber as UserName every single file on the harddrive get an uniqe name. No naming collision and if a customer refers to a drawing it is uniqe. I can get the CodeGen to get UserName into PartNumber or Description but not the other way around. Any tips? /micke UserName.zip
-
Hi I use Innovative Part mode. I like it. Yesterday I got a realy usefull tip about how to use "Assosiate BREP with body" from dleczynski. That function is very powerfull and will save me hours in some cases but it only works on Structural Parts. So based on that. Just asking because I have found that this forum have a skilled userbase with a lot of experience. If I and other beginners know more we will get more out of IC. I haven´t heard or read any good (in my opinion) articles from people with experiense why they use this or that. What do you use and why? Benefits? Is it only a matter of taste? Do any of them have more functions? Is there any performance difference? Do you work with mixed enviroments? Issues? /micke
-
Robosim looks easy and fast to work with. Hopefully IC make an similar solution.
-
Amasing!
-
Hi Interesting. That explains why it is there. In Sweden we in general use ISO 2768. Some companies has their own standards and I even know that some depends on the trailing zeros. When you use trailing zeros is´t it many values that needs to be tinkered with? When using ISO 2768 the tolerance depends on the lenght. In my example with a 32mm value it gives the precision of 32+/-0,2 with 2768-m. If it is a part that need higher tolerances in general I can apply 2768-f which gives 32+-0,15. If the length is 315-1000mm then the deviation is +/-0,8 resp +/-0,3. Is it the same with holes and shafts? For a 10mm hole I would say 10H7 to dimension a hole with a tolerance for a guide pin. It gives me a hole with the limits 10,000 and 10,015. Do you put trailing zeros there as well?
-
Hi Just a question which is´t IronCAD specific. I´ve been learned that trailing zeros does´t add any value. In math it does but not in mechanical drawing/design. When I wan´t to describe the degree of deviation from a value I use tolerances. Sometimes it is a +- value. General dimension values refeer to a standard like ISO 2768. Do you have different ways to define a tolerance value in US? For me the precision option in Drawing is strange and out of use. We have general tolerances like ISO 2768 for mechanical design and ISO 13920 that handles welded constructions. For me 32 and 32,00 is the same value and if the drawing refeers to ISO 2768-m both has a tolerated deviation +-0,2. Do you have different ways of handling tolerances? For me the precision option is a bad habbit of controlling deviations (deviations are controlled by standards). What is your opinion? Just want to understand how other people works and why it is there. /micke
-
Hi Eric Earlier I had performance issues. But that was one complex part with many features. Arfer the support gave the tips to turn of kernel collabration load time went from 12 min to 30 seconds. /micke