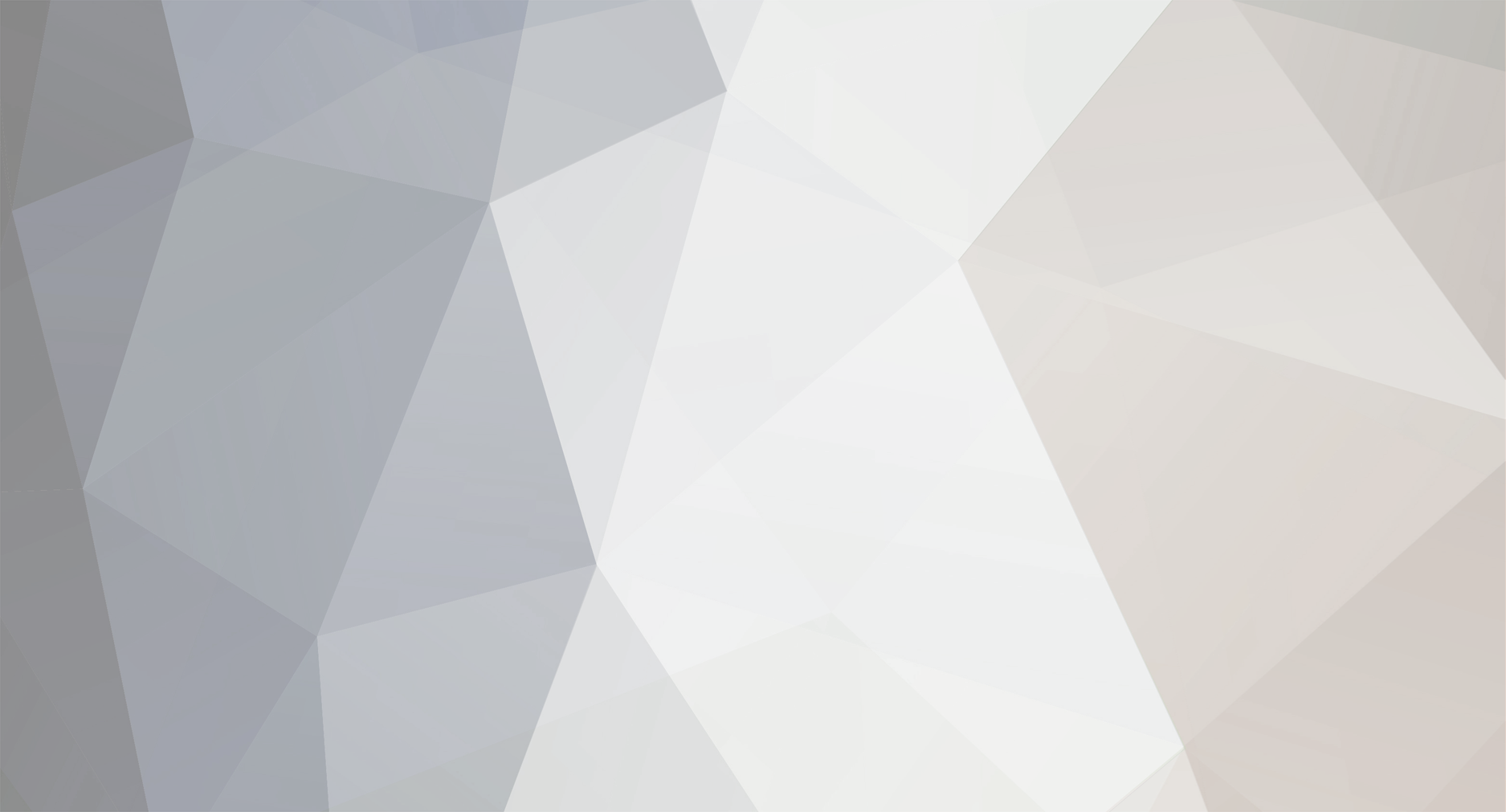
mwalls558626
Community Members-
Posts
233 -
Joined
-
Last visited
Content Type
Profiles
Forums
Blogs
Downloads
Articles
Gallery
Everything posted by mwalls558626
-
I'm 100% behind this getting updated. It is such an everyday thing that really should get updated. To me, anything that a user has to work around everyday, should be prioritized to get updated. I've just lived with it for so long, that I just accept it, but it really is a constant Pain In the A$$. Mike
-
How to create a bend on curve for sheet metal?
mwalls558626 replied to Bart's topic in General Discussion
You would have to use a Form Tool to get that shape, as bends can only be done on straight edges. I'm sure IC support can help with that. If I get any time, I'll do some testing..... Mike -
Tom, I have found that changing the anchor orientation will do the trick. I'll have to look again, but it seems like it pays attention to the Intellishape anchor, if I remember correctly. I had a time where I was doing this a lot, and it seems like I remember solving it by changing the orientation of the Intellishape anchor. I'll try find some time to refresh my memory. Mike
-
Carlo, You don't have to save and close the file, just go to "Shape" then "Recreate Display" and the green highlight will go away. Mike
-
Sheetmetal bend reliefs - left or right choice
mwalls558626 replied to HDEAR's topic in General Discussion
+3 Colors would be great. This has always been a pain in the donkey! -
Kevin, This link only took me to the page to start a trial of IC-Mech. I already have it, and just want to find a breakdown of the functions if possible. Did I skip over something? What Tom had was more what I was looking for, but I'm sure that is outdated because it is still IronProXT. I was just hoping to see a more recent breakdown. Mike
-
I want to add my .02 worth on this thread. I was always wondering if it was just me, but does anyone know a "place" to go to check if there are updates available for the IC Mechanical package? This has always been very frustrating as to how a person can find out if they have the latest version. There may be a simple solution available for this, but I sure don't know what it is. Maybe just a pinned notice in the support community site, with a link to go get it would be nice. Just a thought. Also, I love all the things that IC Mech provides, but I'm sure I only use a small part of what it does because I just don't know what all the features do. It seems like there was something out there that had a breakdown of the functions available, but I don't remember how to get to it if it was out there. If there isn't something like that, there needs to be something that gives an example of each function so a person can start using all of the features. Mike
-
Default Part Size on drop into scene
mwalls558626 replied to mwalls558626's topic in General Discussion
Thanks Cary, I blew right over that when I was poking around. Getting old is becoming less and less fun!!) -
I know how to change the default part size for a sheet metal part when you drop it into a scene, but I could not find where to change the default size for a regular part. I've been using this stuff so long I am forgetting things, but I could not find out if this was even an option. If this is not available now, I would like to turn this into a feature request to be able to control the default size of a block, or any other part, when dropping into a scene. Mike
-
If you are running Win10pro, there could have been an update for NVidia that loaded. It happened with me. Does it with no warning. Why Microsoft is messing with my video drivers, I'll never know. One day all was well, the next day on the same model, it slowed to a crawl. I went to NVidia's site and downloaded the latest drivers, and it fixed the issue. Just throwing things out there. Mike
-
Eric, I'm with you on the legacy interface. I don't know what I would do if they ever stop making it available. It is too bad that IC caved in to the "Ribbon" interface. I get that it is more familiar with new people coming from the other CAD systems, but the legacy interface is one of the main things that makes IC faster than the others. I like one click instead, if possible.....bad memories of ProE and the 10 deep menu's I guess.....done, done, done, etc............ Mike
-
Working with Sheetmetal Fabricators WorkFlow?
mwalls558626 replied to tlehnhaeuser's topic in General Discussion
I have been doing sheet metal parts for a long time, both as an outside person needing a sheet metal part built, and also from the side of being the one that bends it. So, simply put, in order for a sheet metal shop to be able to use a flat pattern generated thru Ironcad, you would have to know the tooling being used. You can't just bend up a sheet metal part, flatten it out, and expect it to universally work at all shops. The reason this is so, is because if it is put in a press brake, they could be using an open air V die, or a coining type die, and these will give different Corner Radius results, just because of how they work, let alone the fact that you can get different corner radius tooling on either style of tooling. The sharper the corner, the larger the flat pattern will have to be to provide enough material to get your desired result. This is easy to confirm by taking any flat piece, make any style bend, and make a copy of it. Then just go into the radius, make them different, and note the change in flat pattern size. I understand that with sheet metal parts, the tolerances are less than typical machined parts, but I can tell you from experience, the more bends you have on a sheet metal part, the more you will see the error stack up, and that will make everyone involved miserable. No one likes to see bad parts made. Mike -
Don't forget the "cut-sheetmetal" function also. This always works in these situations. Mike
-
Love them......Been using a spacemouse almost since they came out. Would not do CAD without one. I personally own 5 of them. A couple are obsolete now, but they have been worth every penny in my opinion. Mike
-
Yes, that is exactly what I was trying to explain. Good job figuring it out. It is not always easy to put down verbally, something that is so visual! I hope that works well for you. Mike
-
Have to chime in just a little on this one. I do a lot of sheet metal parts, and I don't worry about what type of bend I use to build my part, because I want to take advantage of how the InBend, and OutBend work as I am creating the sheet metal part using other existing geometry as reference points. If you have the Auto Constrain on that bend, which is a good default most of the time, you will have to drill down to the intellishape level of the bend, Right Click on the blue constraint that will be showing for the bend, and "Unlock" the constraint of the bend so you can "pull back" the stock material without moving the entire bend feature. The constraint will be there if needed later, just not locked. So what I do is build my sheet metal part using whatever bend type I want, then go back to the corners and check to see if they have any extra stock there, and if they do, I unlock the constraint on the bend, and pull the base material back to the tangent point of the bend radius. More often than not, all you will have to do is pull back one side, and it will, by default, correct for the 2 sides perpendicular to that bend if they are an issue. Mike
-
H Slots and H Cylinders on unfolds not showing
mwalls558626 replied to HDEAR's topic in General Discussion
You can also make any custom shape "punch" you like as a solid part, place it on the cylinder where it needs to be, and then use the "Cut Sheet Metal Part" command to make a hole in the part that is the same shape as the solid punch shape you made. You do this by: 1) Selecting the cylinder at the Part Level (blue outline) 2) Hold the Shift key down and then Left Mouse Button pick the custom punch shape 3) Hit the "Cut Sheet Metal Part" command, and the cylinder will now have the custom punch shape removed from it. You'll have to hide or suppress the shape to see it, but the cut will be there. I can't imagine a more precise way to put the shape you want on a cylinder, and then get a good flat pattern. That being said, it would be real nice to be able to put cuts, or bend lines, into a flat piece, and then fold or roll it up after. Mike -
H Slots and H Cylinders on unfolds not showing
mwalls558626 replied to HDEAR's topic in General Discussion
Kev, Unless I'm missing something, the part in question is a cylindrical shape ( 1000mm diameter) when in use. On this part there are some cutouts. It also sounds like the part is going to be rolled, so it will be in a flat condition before rolling, and they want to put the cutouts into it while it is flat. In that case, why can't the part be made from a piece of Conic Stock with the same radius top and bottom? Then, just put all the cutouts into the Conic Stock shape, and then unfold it for locations of cutouts in flat condition. I do this all the time...... Mike -
H Slots and H Cylinders on unfolds not showing
mwalls558626 replied to HDEAR's topic in General Discussion
Quick question....Is there a reason you cannot put the cutouts into the round shape part before unfolding? Seems to me that if the part is going to be a cylinder when it is in use, you should put the cutouts into the cylindrical shape, and then when you unfold it, you'll know where the holes need to be in Flat Pattern. I may have missed something here....... Mike -
Just a note to all using Sheet Metal Loft. What I have found is that if you are doing the Loft function in sheet metal, you need to make sure your flat pattern is true, to the normal x,y,z coordinate system, in order to get the bend line information to come out correctly. If there is any "angle" to the flat pattern, looking at the thickness of the sheet metal, away from a normal xyz coordinate system, you will not get the bend line information to come out correctly. If you take the flat pattern and make a quick drawing with the 3 normal views, then if you look at the view that looks normal to what would be the thickness of the material, and it is not straight along the axis, you will more than likely not get the bend info on the sheet. Mike
-
Passing a decal in a 3D PDF would be useful too. Any chance of that being implemented? Mike
-
I agree Eric, legacy interface is the best! I hope we won't have to start a "Save the Legacy Interface" movement in the future. Mike
-
Nice!!!
-
Tom, Can't see a much better way than what you did. A long time ago I, and others, asked for a way to model sheetmetal from in the flat state. In other words, take a flat piece of stock, add a bend line across the surface, just like you want to do, and then have the sheetmetal bend across the bend line that was drawn when in the flat state. I have had many tapered parts I needed to make, and this feature would have been very valuable and powerful in that case. I'll poke around as time allows to see what can be done. Mike
-
IC2011 Customization in IC2012 / 3D Mouse Support
mwalls558626 replied to mgajewski's topic in General Discussion
Mark, I use a Space Pilot, and a Space Pilot Pro in both versions. No problems, except for the always present Zoom speed issue. This just needs to be looked into more closely. It is kind of clunky with the zoom when you are close into the part. Needs to be smoother. Mike